CNC гравиращите машини са опитни в прецизната обработка с малки инструменти и притежават способността за фрезоване, шлайфане, пробиване и високоскоростно нарязване.Те се използват широко в различни области като 3C индустрията, производството на мухъл и медицинската индустрия.Тази статия събира често срещани въпроси относно обработката на CNC гравиране.
Какви са основните разлики между CNC гравиране и CNC фрезоване?
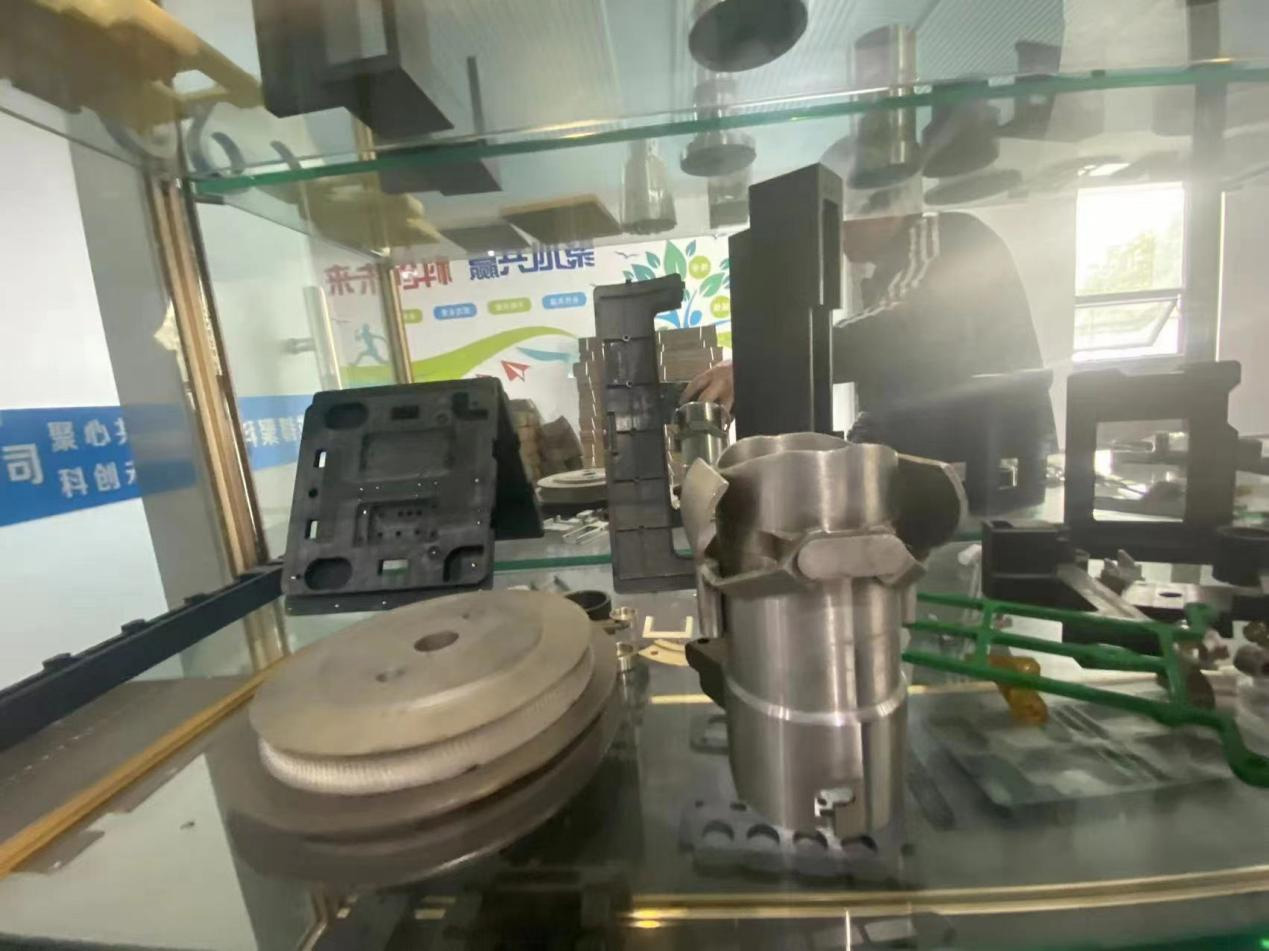
Процесите на CNC гравиране и CNC фрезоване използват принципи на фрезоване.Основната разлика е в използвания диаметър на инструмента, като често използваният диапазон на диаметъра на инструмента за CNC фрезоване варира от 6 до 40 милиметра, докато диаметърът на инструмента за обработка на CNC гравиране варира от 0,2 до 3 милиметра.
Може ли CNC фрезоването да се използва само за груба обработка, докато CNC гравирането може да се използва само за прецизна обработка?
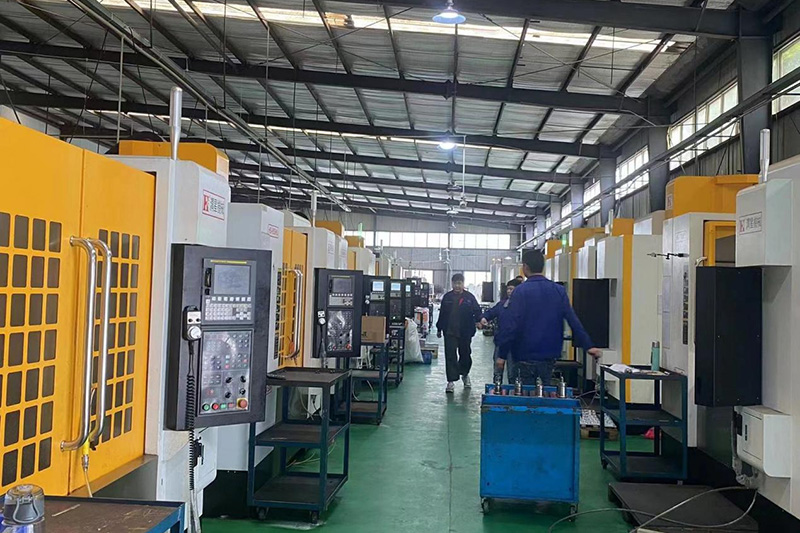
Преди да отговорим на този въпрос, нека първо разберем концепцията на процеса.Обемът на обработка при груба обработка е голям, докато обемът на обработка при прецизна обработка е малък, така че някои хора обичайно смятат грубата обработка за „тежко рязане“, а прецизната обработка като „леко рязане“.Всъщност грубата обработка, полупрецизната обработка и прецизната обработка са концепции за процес, които представляват различни етапи на обработка.И така, точният отговор на този въпрос е, че CNC фрезоването може да направи тежко рязане или леко рязане, докато CNC гравирането може да направи само леко рязане.
Може ли процесът на CNC гравиране да се използва за груба обработка на стоманени материали?
Преценката дали CNC гравирането може да обработи определен материал зависи главно от това колко голям инструмент може да се използва.Режещите инструменти, използвани при обработката на CNC гравиране, определят неговия максимален капацитет на рязане.Ако формата на матрицата позволява използването на инструменти с диаметър над 6 милиметра, силно се препоръчва първо да използвате CNC фрезоване и след това да използвате резба, за да отстраните останалия материал.
Може ли добавянето на глава с увеличаване на скоростта към шпиндела на CNC обработващия център да завърши обработката на гравирането?
Не може да се завърши.Този продукт се появи на изложба преди две години, но не беше възможно да се завърши процесът на дърворезба.Основната причина е, че дизайнът на обработващите центрове с ЦПУ отчита тяхната собствена гама инструменти и цялостната структура не е подходяща за обработка на гравиране.Основната причина за тази погрешна идея е, че те погрешно приемат високоскоростния електрически шпиндел като единствената характеристика на машината за гравиране.
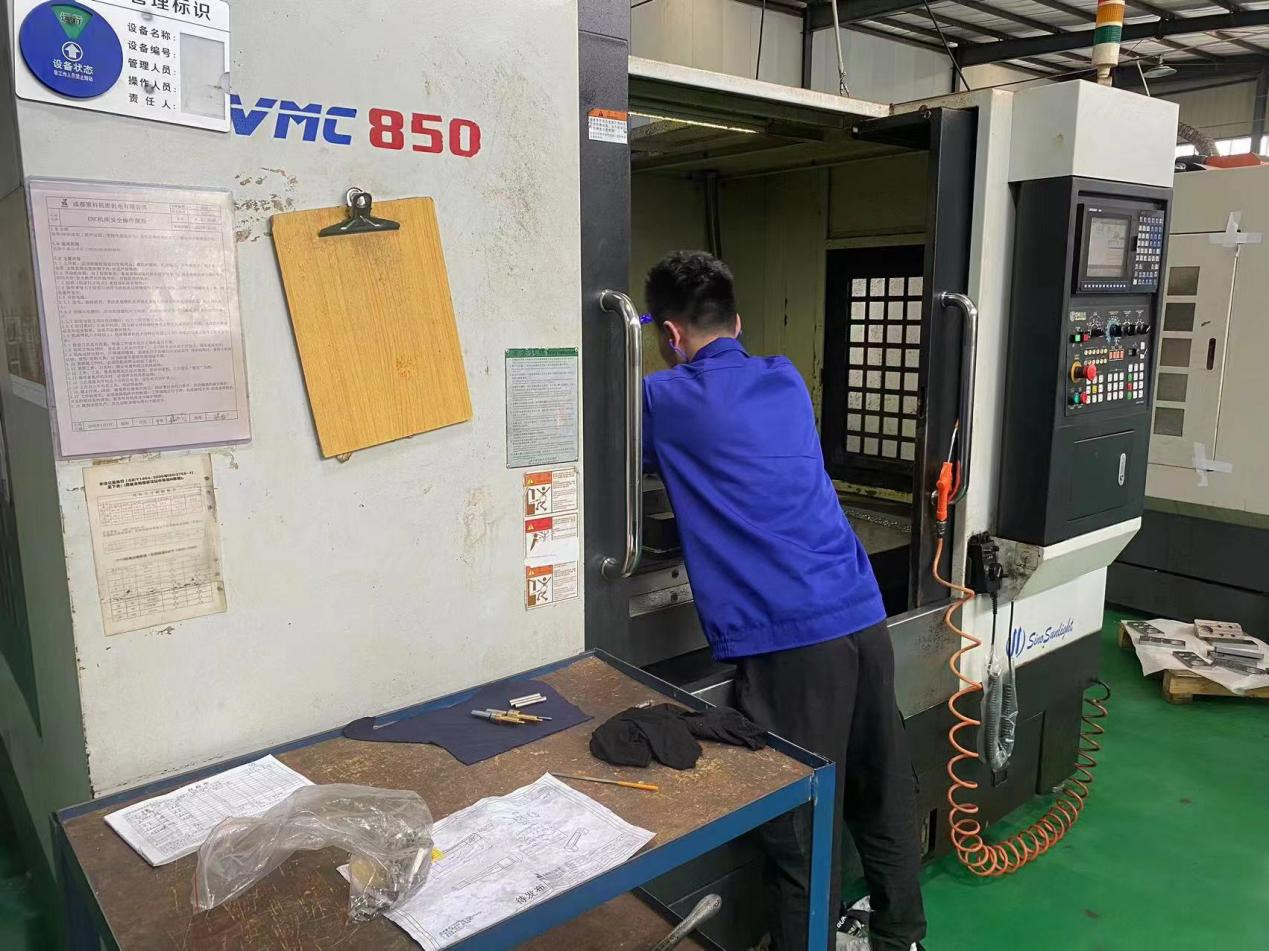
Кои са основните фактори, които влияят върху обработката на резба?
Механичната обработка е сравнително сложен процес и има много фактори, които влияят върху нея, включително следните: характеристики на машинния инструмент, режещи инструменти, системи за управление, характеристики на материала, технология на обработка, спомагателни приспособления и заобикаляща среда.
Какви са изискванията към системата за управление при CNC обработка на гравиране?
Обработката на CNC гравиране е предимно обработка на фрезоване, така че системата за управление трябва да има способността да контролира обработката на фрезоване.За обработка на малки инструменти трябва да се осигури функция за подаване напред, за да се забави пътя предварително и да се намали честотата на счупване на инструмента.В същото време е необходимо да се увеличи скоростта на рязане в относително гладки сегменти на пътя, за да се подобри ефективността на обработката на гравирането.
Какви характеристики на материалите ще повлияят на обработката?
Основните фактори, влияещи върху характеристиките на дърворезбата на материалите, са вид материал, твърдост и издръжливост.Категориите материали включват метални материали и неметални материали.Като цяло, колкото по-висока е твърдостта, толкова по-лоша е обработваемостта, докато колкото по-висок е вискозитетът, толкова по-лоша е обработваемостта.Колкото повече примеси, толкова по-лоша е обработваемостта и толкова по-голяма е твърдостта на частиците вътре в материала, което води до по-лоша обработваемост.Общият стандарт е: колкото по-високо е съдържанието на въглерод, толкова по-лоша е обработваемостта, колкото по-високо е съдържанието на сплав, толкова по-лоша е обработваемостта, и колкото по-високо е съдържанието на неметални елементи, толкова по-добра е обработваемостта (но съдържанието на неметали като цяло материалите се контролират строго).
Какви материали са подходящи за обработка на резба?
Неметалните материали, подходящи за дърворезба, включват органично стъкло, смола, дърво и др. Неметалните материали, които не са подходящи за дърворезба, включват естествен мрамор, стъкло и др. Подходящите метални материали за дърворезба включват мед, алуминий и мека стомана с твърдост под HRC40 , докато неподходящите метални материали за дърворезба включват закалена стомана и др.
Какво е влиянието на самия режещ инструмент върху процеса на обработка и как му влияе?
Факторите на режещия инструмент, които влияят на обработката на гравирането, включват материал на инструмента, геометрични параметри и технология на шлайфане.Материалът на режещия инструмент, използван при обработката на резба, е материал от твърда сплав, който е прахова сплав.Основният показател за ефективност, който определя производителността на материала, е средният диаметър на праха.Колкото по-малък е диаметърът, толкова по-устойчив на износване е инструментът и толкова по-висока ще бъде издръжливостта на инструмента.Повече знания за NC програмиране се фокусират върху официалния акаунт в WeChat (обучение по NC програмиране), за да получите урока.Остротата на инструмента влияе главно върху силата на рязане.Колкото по-остър е инструментът, толкова по-ниска е силата на рязане, толкова по-гладка е обработката и по-високо е качеството на повърхността, но толкова по-ниска е издръжливостта на инструмента.Следователно при обработката на различни материали трябва да се избира различна острота.При обработка на меки и лепкави материали е необходимо режещият инструмент да се заточи.Когато твърдостта на обработвания материал е висока, остротата трябва да се намали, за да се подобри издръжливостта на режещия инструмент.Но не може да бъде твърде тъп, в противен случай силата на рязане ще бъде твърде голяма и ще повлияе на обработката.Ключовият фактор при шлифоването на инструменти е размерът на отворите на прецизния шлифовъчен диск.Шлифовъчен диск с голяма мрежа може да произведе по-фини режещи ръбове, което ефективно подобрява издръжливостта на режещия инструмент.Шлифовъчните колела с голям размер на отворите могат да произвеждат по-гладки странични повърхности, което може да подобри качеството на повърхността на рязане.
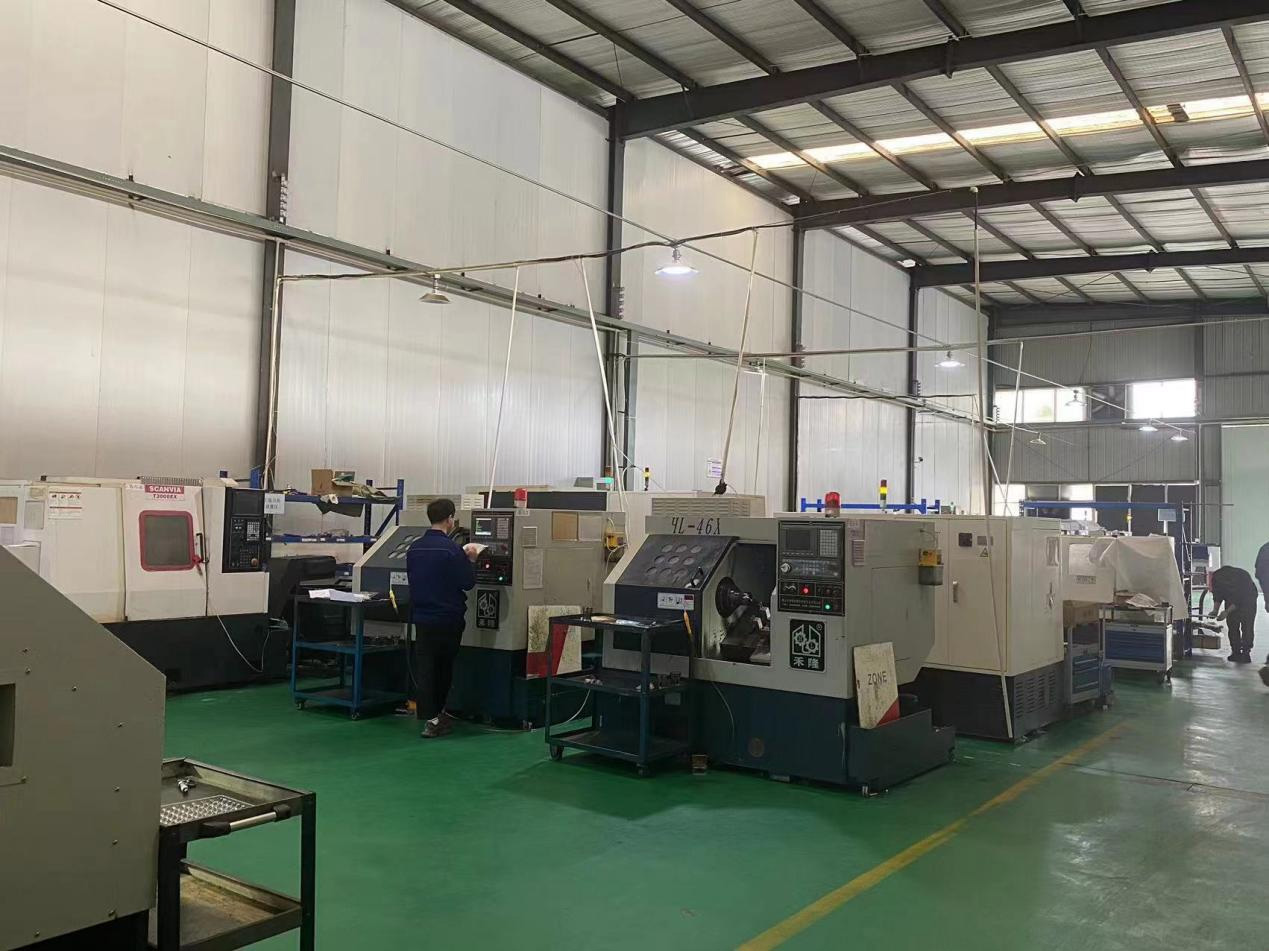
Каква е формулата за живота на инструмента?
Животът на инструмента се отнася главно до живота на инструмента по време на обработката на стоманени материали.Емпиричната формула е: (T е животът на инструмента, CT е параметърът на живота, VC е скоростта на линията на рязане, f е дълбочината на рязане за оборот и P е дълбочината на рязане).Скоростта на линията на рязане има най-голямо влияние върху живота на инструмента.В допълнение, радиалното биене на инструмента, качеството на шлифоване на инструмента, материалът и покритието на инструмента и охлаждащата течност също могат да повлияят на издръжливостта на инструмента.
Как да защитим оборудването на резбарската машина по време на обработката?
1) Защитете устройството за настройка на инструмента от прекомерна ерозия на маслото.
2) Обърнете внимание на контрола на летящите отломки.Летящите отломки представляват голяма заплаха за машината.Летенето в електрическия контролен шкаф може да причини късо съединение, а летенето във водещата релса може да намали живота на винта и водещата релса.Следователно по време на обработката основните части на машинния инструмент трябва да бъдат правилно запечатани.
3) Когато местите осветлението, не дърпайте капачката на лампата, тъй като може лесно да я повредите.
4) По време на процеса на обработка не се доближавайте до зоната на рязане за наблюдение, за да избегнете летящи отломки, които могат да повредят очите.Когато моторът на шпиндела се върти, е забранено да се извършват каквито и да е операции на работната маса.
5) Когато отваряте и затваряте вратата на машината, не я отваряйте или затваряйте насила.По време на прецизна обработка, ударът и вибрациите по време на процеса на отваряне на вратата могат да причинят следи от нож върху обработваната повърхност.
6) За да зададете скорост на шпиндела и след това да започнете обработката, в противен случай поради бавното стартиране на шпиндела желаната скорост може да не бъде достигната преди започване на обработката, което води до задушаване на двигателя.
7) Забранено е поставянето на каквито и да било инструменти или детайли върху напречната греда на инструменталната машина.
8) Строго е забранено поставянето на магнитни инструменти, като например магнитни вендузи и държачи за циферблат, върху електрическия контролен шкаф, тъй като това може да повреди дисплея.

Каква е функцията на флуида за рязане?
Обърнете внимание на добавянето на охлаждащо масло по време на обработката на метала.Функцията на охладителната система е да отстранява топлината от рязане и летящите остатъци, осигурявайки смазване за машинна обработка.Охлаждащата течност ще движи режещия ремък, намалявайки топлината, предавана към режещия инструмент и двигателя, и подобрявайки техния експлоатационен живот.Отстранете летящите отломки, за да избегнете вторично рязане.Смазването може да намали силата на рязане и да направи обработката по-стабилна.При обработката на мед използването на мазна течност за рязане може да подобри качеството на повърхността.
Какви са етапите на износване на инструмента?
Износването на режещите инструменти може да бъде разделено на три етапа: първоначално износване, нормално износване и рязко износване.В началния етап на износване основната причина за износване на инструмента е, че температурата на инструмента е ниска и не достига оптималната температура на рязане.По това време износването на инструмента е предимно абразивно износване, което има по-голямо въздействие върху инструмента.Повече знания за програмиране с NC се фокусират върху официалния акаунт на WeChat (обучение по програмиране на цифров контрол), за да получите урока, който лесно може да причини счупване на инструмента.Този етап е много опасен и ако не се работи правилно, може директно да доведе до счупване и повреда на инструмента.Когато инструментът премине първоначалния период на износване и температурата на рязане достигне определена стойност, основното износване е дифузионно износване, което причинява главно локално отлепване.Така че износването е относително малко и бавно.Когато износването достигне определено ниво, инструментът става неефективен и навлиза в период на бързо износване.
Защо и как трябва да се пускат режещите инструменти?
По-горе споменахме, че по време на началния етап на износване инструментът е предразположен към счупване.За да избегнем явлението счупване, трябва да пуснем инструмента.Постепенно увеличавайте температурата на рязане на инструмента до разумна температура.След експериментална проверка бяха направени сравнения с помощта на същите параметри на обработка.Вижда се, че след разработка животът на инструмента се е увеличил повече от два пъти.
Методът на вкарване е да се намали скоростта на подаване наполовина, като същевременно се поддържа разумна скорост на шпиндела, а времето за обработка е приблизително 5-10 минути.Когато обработвате меки материали, вземете малката стойност, а когато обработвате твърди метали, вземете голямата стойност.
Как да определите силното износване на инструмента?
Методът за определяне на силното износване на инструмента е:
1) Слушайте обработващия звук и направете рязко повикване;
2) Слушайки звука на вретеното, има забележим феномен на задържане на вретеното;
3) Усещане, че вибрациите се увеличават по време на обработката и има очевидна вибрация на шпиндела на машинния инструмент;
4) Въз основа на ефекта на обработка, обработената шарка на долния нож може да е добра или лоша (ако това е така в началото, това показва, че дълбочината на рязане е твърде дълбока).
Кога трябва да сменя ножа?
Трябва да сменим инструмента на около 2/3 от срока на живот на инструмента.Например, ако инструментът претърпи силно износване в рамките на 60 минути, следващата обработка трябва да започне смяната на инструмента в рамките на 40 минути и да развиете навика за редовна смяна на инструмента.
Могат ли силно износените инструменти да продължат да се обработват?
След силно износване на инструмента силата на рязане може да се увеличи до три пъти нормалното.Силата на рязане оказва значително влияние върху експлоатационния живот на електрода на шпиндела и връзката между експлоатационния живот на двигателя на шпиндела и силата е обратно пропорционална на третата степен.Например, когато силата на рязане се увеличи три пъти, обработката за 10 минути е еквивалентна на използване на шпиндела за 10 * 33=270 минути при нормални условия.
Как да се определи дължината на удължаване на инструмента по време на груба обработка?
Колкото по-къса е дължината на удължението на инструмента, толкова по-добре.Въпреки това, при действителната обработка, ако е твърде къса, дължината на инструмента трябва да се регулира често, което може значително да повлияе на ефективността на обработката.И така, как трябва да се контролира дължината на удължаване на режещия инструмент при реална обработка?Принципът е следният: φ Лента с инструменти с диаметър 3 може да се обработва нормално чрез удължаване на 5 mm.φ Режещата греда с 4 диаметъра може да се обработва нормално чрез удължаване на 7 mm.φ Режещата греда с 6 диаметър може да се обработва нормално чрез удължаване на 10 mm.Опитайте се да достигнете под тези стойности, когато режете.Ако дължината на горния инструмент е по-голяма от горната стойност, опитайте се да го контролирате до дълбочината на обработка, когато инструментът се износи.Това е малко трудно за разбиране и изисква повече обучение.
Как да се справим с внезапното счупване на инструмента по време на обработка?
1) Спрете обработката и вижте текущия сериен номер на обработката.
2) Проверете дали има счупено острие в точката на рязане и ако е така, отстранете го.
3) Анализирайте причината за счупения инструмент, която е най-важната.Защо инструментът се счупи?Трябва да анализираме различните фактори, които влияят на обработката, споменати по-горе.Но причината за счупения инструмент е, че силата върху инструмента внезапно се увеличава.Или това е проблем с пътя, или има прекомерно трептене на инструмента, или има твърди блокове в материала, или скоростта на двигателя на шпиндела е неправилна.
4) След анализ сменете инструмента за обработка.Ако пътят не е променен, обработката трябва да се извърши с един номер пред първоначалния номер.По това време е необходимо да се обърне внимание на намаляване на скоростта на подаване.Това е така, защото втвърдяването при счупването на инструмента е силно и също така е необходимо да се извърши разработка на инструмента.
Как да коригирате параметрите на обработка, когато грубата обработка не е добра?
Ако животът на инструмента не може да бъде гарантиран при разумна скорост на главната ос, когато регулирате параметрите, първо регулирайте дълбочината на рязане, след това регулирайте скоростта на подаване и след това отново регулирайте скоростта на странично подаване.(Забележка: Регулирането на дълбочината на рязане също има ограничения. Ако дълбочината на рязане е твърде малка и има твърде много слоеве, теоретичната ефективност на рязане може да е висока. Действителната ефективност на обработка обаче се влияе от други фактори, което води до твърде ниска обработка ефективност. В този момент е необходимо да се замени режещият инструмент с по-малък за обработка, но ефективността на обработка е по-висока. Най-общо казано, минималната дълбочина на рязане не може да бъде по-малка от 0,1 mm.).
Време на публикуване: 13 април 2023 г