सीएनसी खोदकाम यंत्रे लहान साधनांसह अचूक मशीनिंगमध्ये कुशल असतात आणि दळणे, ग्राइंडिंग, ड्रिलिंग आणि हाय-स्पीड टॅपिंग करण्याची क्षमता असते.ते 3C उद्योग, साचा उद्योग आणि वैद्यकीय उद्योग यासारख्या विविध क्षेत्रात मोठ्या प्रमाणावर वापरले जातात.हा लेख CNC खोदकाम प्रक्रियेबद्दल सामान्य प्रश्न एकत्रित करतो.
सीएनसी खोदकाम आणि सीएनसी मिलिंगमधील मुख्य फरक काय आहेत?
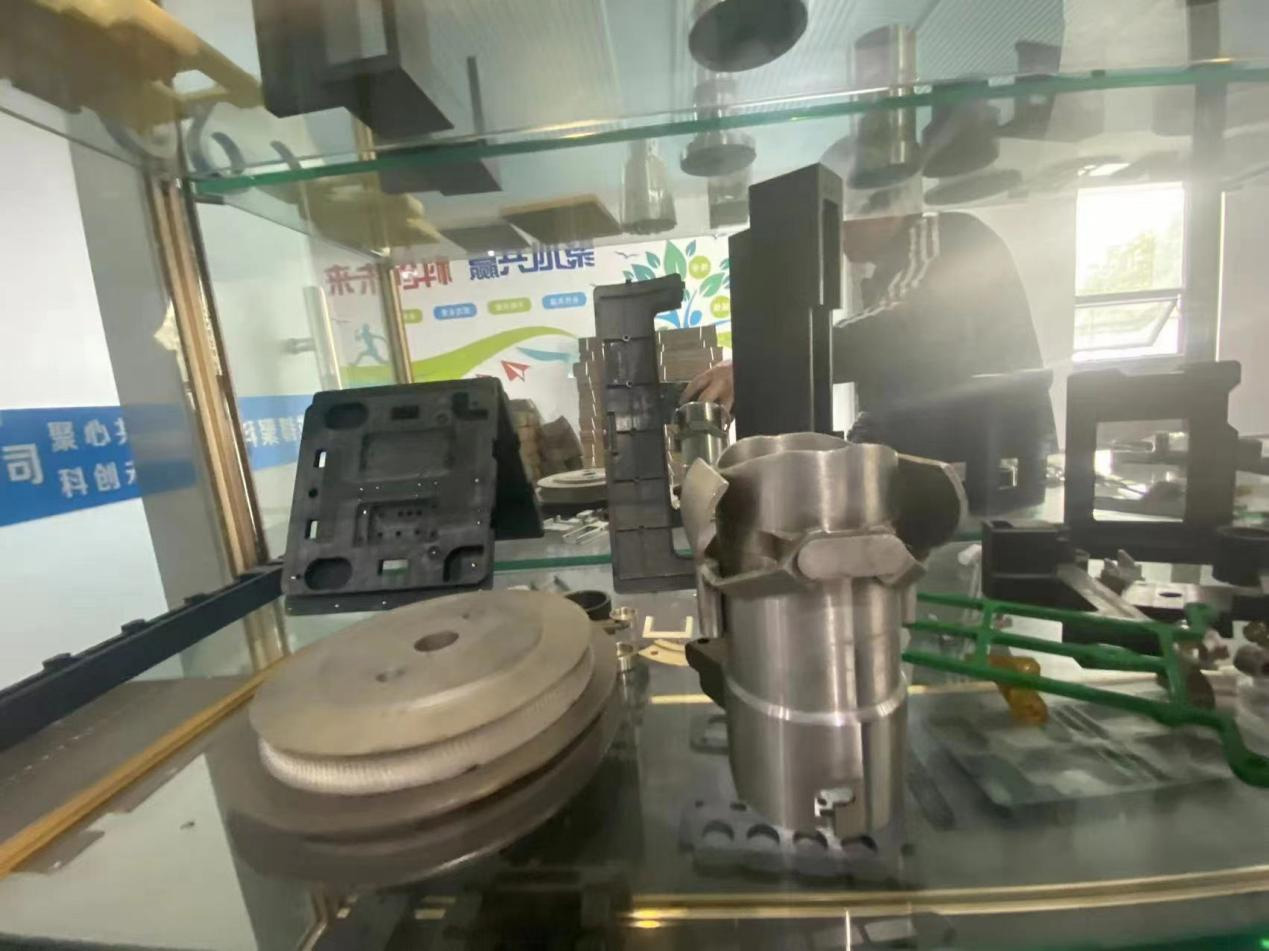
सीएनसी खोदकाम आणि सीएनसी मिलिंग प्रक्रिया दोन्ही मिलिंग तत्त्वे वापरतात.मुख्य फरक वापरलेल्या टूल व्यासामध्ये आहे, सामान्यतः CNC मिलिंगसाठी वापरले जाणारे टूल व्यास 6 ते 40 मिलीमीटर पर्यंत आहे, तर CNC खोदकाम प्रक्रियेसाठी टूल व्यास 0.2 ते 3 मिलीमीटर पर्यंत आहे.
सीएनसी मिलिंग फक्त खडबडीत मशीनिंगसाठी वापरली जाऊ शकते, तर सीएनसी खोदकाम फक्त अचूक मशीनिंगसाठी वापरले जाऊ शकते?
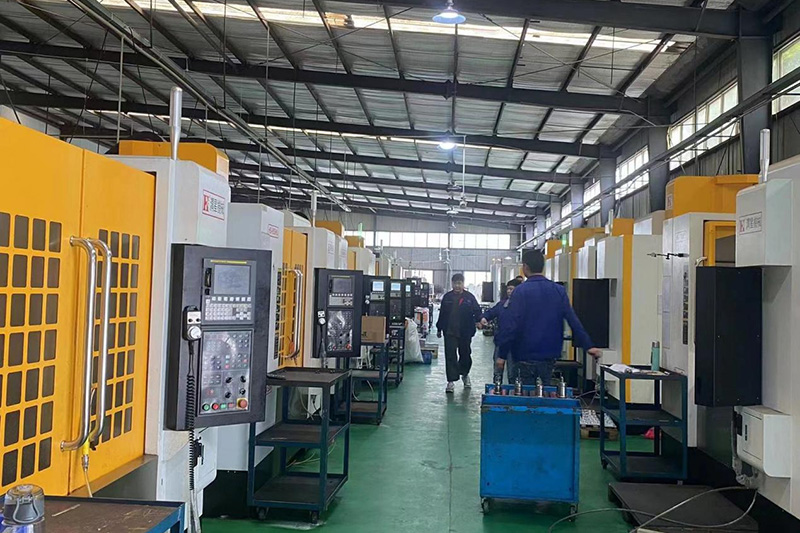
या प्रश्नाचे उत्तर देण्यापूर्वी, प्रथम प्रक्रियेची संकल्पना समजून घेऊ.रफ मशिनिंगचे प्रोसेसिंग व्हॉल्यूम मोठे असते, तर अचूक मशीनिंगचे प्रोसेसिंग व्हॉल्यूम लहान असते, त्यामुळे काही लोक रफ मशीनिंगला "हेवी कटिंग" आणि अचूक मशीनिंग "लाइट कटिंग" मानतात.खरं तर, रफ मशिनिंग, सेमी प्रिसिजन मशिनिंग आणि प्रिसिजन मशीनिंग या प्रक्रिया संकल्पना आहेत ज्या वेगवेगळ्या प्रक्रिया टप्प्यांचे प्रतिनिधित्व करतात.तर, या प्रश्नाचे अचूक उत्तर असे आहे की सीएनसी मिलिंग हेवी कटिंग किंवा हलकी कटिंग करू शकते, तर सीएनसी खोदकाम फक्त हलके कटिंग करू शकते.
स्टील सामग्रीच्या खडबडीत मशीनिंगसाठी सीएनसी खोदकाम प्रक्रिया वापरली जाऊ शकते का?
सीएनसी खोदकाम एखाद्या विशिष्ट सामग्रीवर प्रक्रिया करू शकते की नाही हे ठरवणे हे मुख्यतः एखादे साधन किती मोठे आहे यावर अवलंबून असते.CNC खोदकाम प्रक्रियेत वापरलेली कटिंग टूल्स त्याची कमाल कटिंग क्षमता निर्धारित करतात.जर मोल्डचा आकार 6 मिलिमीटरपेक्षा जास्त व्यास असलेल्या साधनांचा वापर करण्यास अनुमती देत असेल, तर प्रथम सीएनसी मिलिंग वापरण्याची आणि नंतर उर्वरित सामग्री काढण्यासाठी कोरीवकाम वापरण्याची जोरदार शिफारस केली जाते.
सीएनसी मशीनिंग सेंटरच्या स्पिंडलमध्ये स्पीड वाढणारे हेड जोडल्याने खोदकाम प्रक्रिया पूर्ण होऊ शकते?
पूर्ण करण्यात अक्षम.हे उत्पादन दोन वर्षांपूर्वी एका प्रदर्शनात दिसले, परंतु कोरीव काम पूर्ण करणे शक्य झाले नाही.मुख्य कारण म्हणजे CNC मशीनिंग सेंटर्सची रचना त्यांच्या स्वतःच्या टूल श्रेणीचा विचार करते आणि एकूण रचना खोदकाम प्रक्रियेसाठी योग्य नाही.या चुकीच्या कल्पनेचे मुख्य कारण म्हणजे त्यांनी खोदकाम यंत्राचे एकमेव वैशिष्ट्य म्हणून हाय-स्पीड इलेक्ट्रिक स्पिंडल असे समजले.
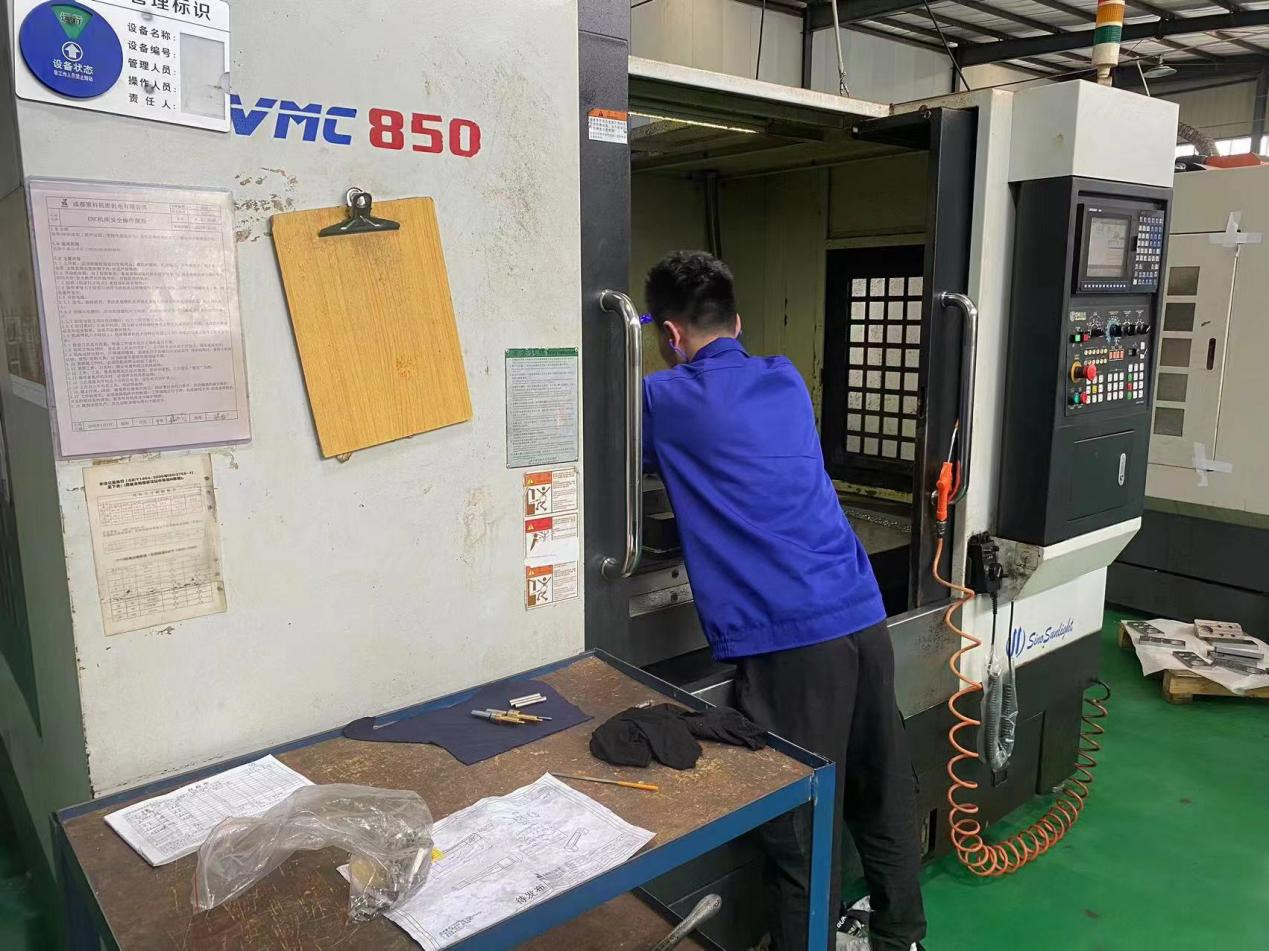
कोरीव प्रक्रियेवर परिणाम करणारे मुख्य घटक कोणते आहेत?
यांत्रिक प्रक्रिया ही एक तुलनेने गुंतागुंतीची प्रक्रिया आहे आणि त्यावर परिणाम करणारे अनेक घटक आहेत, ज्यात प्रामुख्याने खालील गोष्टींचा समावेश होतो: मशीन टूल वैशिष्ट्ये, कटिंग टूल्स, कंट्रोल सिस्टम, सामग्री वैशिष्ट्ये, प्रक्रिया तंत्रज्ञान, सहाय्यक फिक्स्चर आणि आसपासचे वातावरण.
सीएनसी खोदकाम प्रक्रियेत नियंत्रण प्रणालीसाठी कोणत्या आवश्यकता आहेत?
सीएनसी खोदकाम प्रक्रिया प्रामुख्याने मिलिंग प्रक्रिया आहे, म्हणून नियंत्रण प्रणालीमध्ये मिलिंग प्रक्रिया नियंत्रित करण्याची क्षमता असणे आवश्यक आहे.लहान टूल मशिनिंगसाठी, मार्ग अगोदर कमी करण्यासाठी आणि टूल ब्रेकेजची वारंवारता कमी करण्यासाठी फीडफॉरवर्ड फंक्शन प्रदान करणे आवश्यक आहे.त्याच वेळी, खोदकाम प्रक्रियेची कार्यक्षमता सुधारण्यासाठी, तुलनेने गुळगुळीत मार्ग विभागांमध्ये कटिंग गती वाढवणे आवश्यक आहे.
सामग्रीची कोणती वैशिष्ट्ये प्रक्रियेवर परिणाम करतात?
सामग्रीच्या कोरीव कार्यक्षमतेवर परिणाम करणारे मुख्य घटक म्हणजे सामग्रीचा प्रकार, कडकपणा आणि कडकपणा.भौतिक श्रेणींमध्ये धातूचे साहित्य आणि नॉन-मेटलिक साहित्य समाविष्ट आहे.एकंदरीत, कडकपणा जितका जास्त तितकी कार्यक्षमता खराब, तर स्निग्धता जितकी जास्त तितकी कार्यक्षमता खराब.जितकी जास्त अशुद्धता, तितकी खराब कार्यक्षमता आणि सामग्रीच्या आत कणांची कठोरता जास्त, परिणामी खराब कार्यक्षमता.एक सामान्य मानक आहे: कार्बन सामग्री जितकी जास्त, तितकी खराब कार्यक्षमता, मिश्रधातूची सामग्री जितकी जास्त असेल तितकी खराब कार्यक्षमता आणि गैर-धातू घटक सामग्री जितकी जास्त असेल तितकी कार्यक्षमता (परंतु सर्वसाधारणपणे गैर-धातू सामग्री सामग्री कठोरपणे नियंत्रित आहे).
कोरीव प्रक्रियेसाठी कोणती सामग्री योग्य आहे?
कोरीव कामासाठी योग्य नसलेल्या धातू नसलेल्या पदार्थांमध्ये सेंद्रिय काच, राळ, लाकूड इत्यादींचा समावेश होतो. कोरीव कामासाठी योग्य नसलेल्या धातू नसलेल्या पदार्थांमध्ये नैसर्गिक संगमरवरी, काच इत्यादींचा समावेश होतो. कोरीव कामासाठी योग्य धातूंच्या साहित्यात तांबे, अॅल्युमिनियम आणि HRC40 पेक्षा कमी कडकपणा असलेले मऊ स्टील यांचा समावेश होतो. , तर कोरीव कामासाठी अयोग्य धातूच्या साहित्यात विझलेले स्टील इ.
मशीनिंग प्रक्रियेवर कटिंग टूलचा स्वतःचा काय परिणाम होतो आणि त्याचा कसा परिणाम होतो?
खोदकाम प्रक्रियेवर परिणाम करणारे कटिंग टूल घटकांमध्ये टूल मटेरियल, भौमितिक पॅरामीटर्स आणि ग्राइंडिंग तंत्रज्ञान यांचा समावेश होतो.कोरीव प्रक्रियेत वापरले जाणारे कटिंग टूल मटेरियल हार्ड अॅलॉय मटेरियल आहे, जे पावडर मिश्र धातु आहे.मुख्य कार्यप्रदर्शन निर्देशक जे सामग्रीचे कार्यप्रदर्शन निर्धारित करते ते पावडरचा सरासरी व्यास आहे.व्यास जितका लहान असेल तितके उपकरण अधिक पोशाख-प्रतिरोधक असेल आणि उपकरणाची टिकाऊपणा जितकी जास्त असेल.अधिक NC प्रोग्रामिंग ज्ञान ट्यूटोरियल मिळविण्यासाठी WeChat अधिकृत खाते (NC प्रोग्रामिंग शिकवण्या) वर केंद्रित आहे.टूलची तीक्ष्णता प्रामुख्याने कटिंग फोर्सवर परिणाम करते.टूल जितके तीक्ष्ण असेल तितकी कटिंग फोर्स कमी, प्रक्रिया गुळगुळीत आणि पृष्ठभागाची गुणवत्ता जितकी जास्त असेल, परंतु टूलची टिकाऊपणा कमी असेल.म्हणून, वेगवेगळ्या सामग्रीवर प्रक्रिया करताना भिन्न तीक्ष्णता निवडली पाहिजे.मऊ आणि चिकट पदार्थांवर प्रक्रिया करताना, कटिंग टूलला तीक्ष्ण करणे आवश्यक आहे.जेव्हा प्रक्रिया केलेल्या सामग्रीची कठोरता जास्त असते, तेव्हा कटिंग टूलची टिकाऊपणा सुधारण्यासाठी तीक्ष्णता कमी केली पाहिजे.परंतु ते खूप बोथट असू शकत नाही, अन्यथा कटिंग फोर्स खूप मोठे असेल आणि मशीनिंगवर परिणाम करेल.टूल ग्राइंडिंगमधील महत्त्वाचा घटक म्हणजे अचूक ग्राइंडिंग व्हीलचा जाळीचा आकार.उच्च जाळीचे ग्राइंडिंग व्हील अधिक बारीक कटिंग धार तयार करू शकते, ज्यामुळे कटिंग टूलची टिकाऊपणा प्रभावीपणे सुधारते.उच्च जाळीच्या आकारासह चाके ग्राइंड केल्याने नितळ बाजूचे पृष्ठभाग तयार होऊ शकतात, ज्यामुळे कटिंगच्या पृष्ठभागाची गुणवत्ता सुधारू शकते.
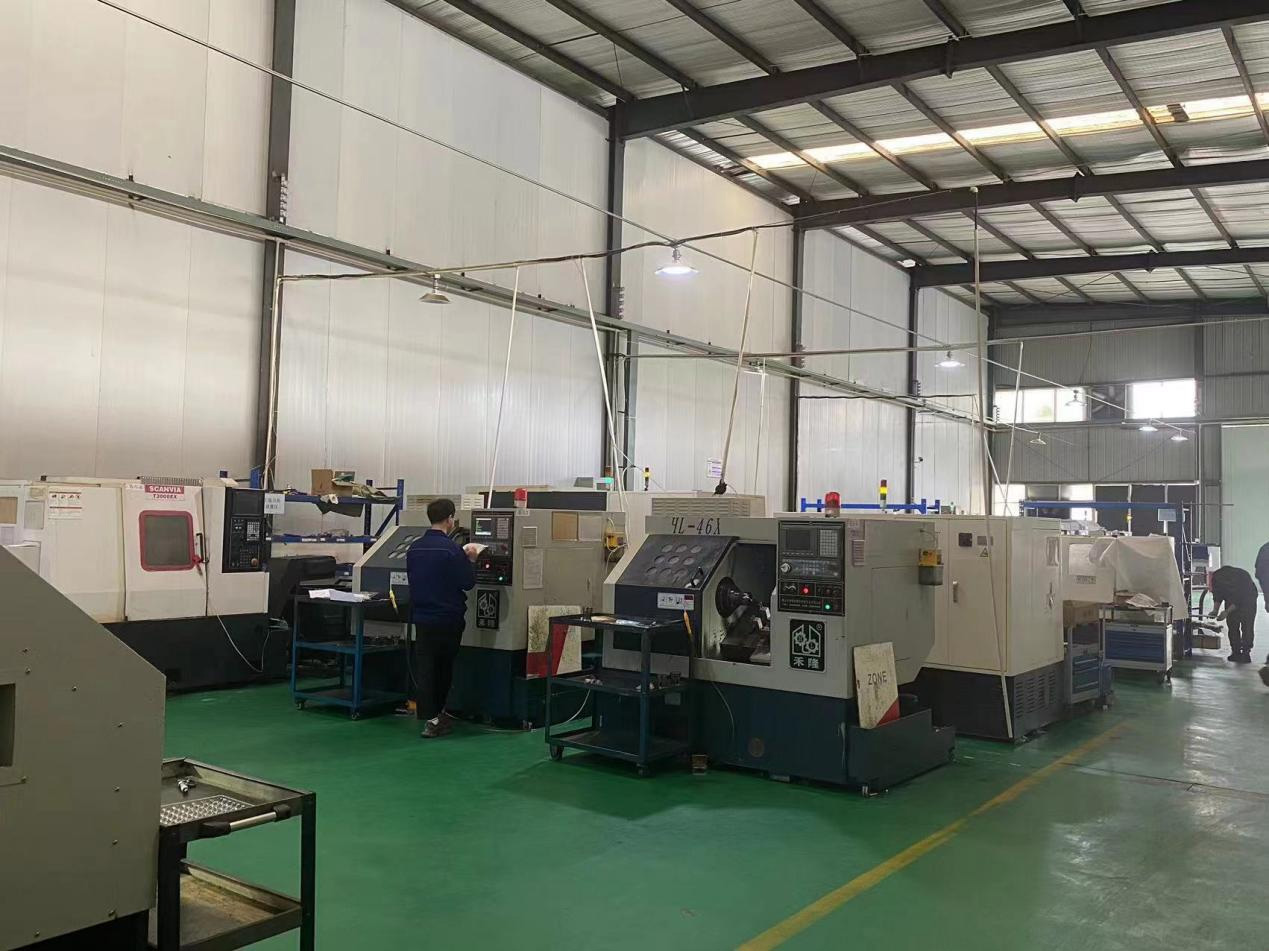
साधन जीवनासाठी सूत्र काय आहे?
टूल लाइफ मुख्यतः स्टील सामग्रीच्या प्रक्रियेदरम्यान टूल लाइफचा संदर्भ देते.प्रायोगिक सूत्र आहे: (टी हे टूल लाइफ आहे, सीटी हे लाइफ पॅरामीटर आहे, व्हीसी ही कटिंग लाइन स्पीड आहे, f ही कटिंग डेप्थ प्रति क्रांती आहे आणि P ही कटिंग डेप्थ आहे).कटिंग लाइन स्पीडचा टूल लाइफवर सर्वाधिक प्रभाव पडतो.याव्यतिरिक्त, टूल रेडियल रनआउट, टूल ग्राइंडिंग गुणवत्ता, टूल सामग्री आणि कोटिंग आणि शीतलक देखील टूलच्या टिकाऊपणावर परिणाम करू शकतात.
प्रक्रियेदरम्यान कोरीव मशीन उपकरणांचे संरक्षण कसे करावे?
1) जास्त तेल धूप पासून टूल सेटिंग डिव्हाइसचे संरक्षण करा.
२) उडणाऱ्या भंगाराच्या नियंत्रणाकडे लक्ष द्या.उडणाऱ्या ढिगाऱ्यांमुळे मशीन टूलला मोठा धोका निर्माण होतो.इलेक्ट्रिकल कंट्रोल कॅबिनेटमध्ये उड्डाण केल्याने शॉर्ट सर्किट होऊ शकते आणि मार्गदर्शक रेल्वेमध्ये उड्डाण केल्याने स्क्रू आणि मार्गदर्शक रेल्वेचे आयुष्य कमी होऊ शकते.म्हणून, प्रक्रिया करताना, मशीन टूलचे मुख्य भाग योग्यरित्या सील केले पाहिजेत.
3) लाइटिंग हलवताना, दिव्याची टोपी ओढू नका कारण यामुळे दिव्याच्या टोपीला सहजपणे नुकसान होऊ शकते.
4) मशीनिंग प्रक्रियेदरम्यान, डोळ्यांना इजा होऊ शकणारे उडणारे ढिगारे टाळण्यासाठी निरीक्षणासाठी कटिंग क्षेत्राकडे जाऊ नका.स्पिंडल मोटर फिरत असताना, वर्कबेंचवर कोणतेही ऑपरेशन करण्यास मनाई आहे.
5) मशीन टूल दरवाजा उघडताना आणि बंद करताना, जबरदस्तीने उघडू किंवा बंद करू नका.अचूक मशीनिंग दरम्यान, दरवाजा उघडण्याच्या प्रक्रियेदरम्यान होणारा प्रभाव आणि कंपन प्रक्रिया केलेल्या पृष्ठभागावर चाकूच्या खुणा होऊ शकतात.
6) स्पिंडलला गती देणे आणि नंतर प्रक्रिया सुरू करणे, अन्यथा स्पिंडलच्या संथ सुरुवातीमुळे, प्रक्रिया सुरू करण्यापूर्वी इच्छित वेग गाठला जाऊ शकत नाही, ज्यामुळे मोटर गुदमरते.
7) मशीन टूलच्या क्रॉसबीमवर कोणतीही साधने किंवा वर्कपीस ठेवण्यास मनाई आहे.
8) चुंबकीय उपकरणे जसे की चुंबकीय सक्शन कप आणि डायल गेज होल्डर इलेक्ट्रिक कंट्रोल कॅबिनेटवर ठेवण्यास सक्त मनाई आहे, कारण यामुळे डिस्प्ले खराब होऊ शकतो.

द्रव कापण्याचे कार्य काय आहे?
मेटल प्रोसेसिंग दरम्यान कूलिंग ऑइल जोडण्याकडे लक्ष द्या.शीतकरण प्रणालीचे कार्य कटिंग उष्णता आणि उडणारे मलबे काढून टाकणे, मशीनिंगसाठी स्नेहन प्रदान करणे आहे.शीतलक कटिंग बेल्ट हलवेल, कटिंग टूल आणि मोटरमध्ये हस्तांतरित होणारी उष्णता कमी करेल आणि त्यांचे सेवा जीवन सुधारेल.दुय्यम कटिंग टाळण्यासाठी उडणारा मलबा काढून टाका.स्नेहन कटिंग फोर्स कमी करू शकते आणि मशीनिंग अधिक स्थिर बनवू शकते.तांब्याच्या प्रक्रियेत, तेलकट कटिंग द्रव वापरल्याने पृष्ठभागाची गुणवत्ता सुधारू शकते.
टूल पोशाखचे टप्पे काय आहेत?
कटिंग टूल्सचा पोशाख तीन टप्प्यात विभागला जाऊ शकतो: प्रारंभिक पोशाख, सामान्य पोशाख आणि तीक्ष्ण पोशाख.सुरुवातीच्या पोशाख अवस्थेत, टूल परिधान करण्याचे मुख्य कारण म्हणजे टूलचे तापमान कमी असते आणि ते इष्टतम कटिंग तापमानापर्यंत पोहोचत नाही.यावेळी, टूल पोशाख मुख्यतः अपघर्षक पोशाख असतो, ज्याचा टूलवर जास्त प्रभाव पडतो.अधिक NC प्रोग्रामिंग ज्ञान ट्यूटोरियल प्राप्त करण्यासाठी WeChat अधिकृत खात्यावर (डिजिटल कंट्रोल प्रोग्रामिंग शिकवण्यावर) लक्ष केंद्रित करते, जे टूल तुटणे सोपे आहे.हा टप्पा अतिशय धोकादायक आहे आणि जर ते योग्यरित्या हाताळले नाही तर ते थेट साधन तुटणे आणि अयशस्वी होऊ शकते.जेव्हा साधन प्रारंभिक पोशाख कालावधी पास करते आणि कटिंग तापमान एका विशिष्ट मूल्यापर्यंत पोहोचते, तेव्हा मुख्य पोशाख हा प्रसार पोशाख असतो, ज्यामुळे मुख्यतः स्थानिक सोलणे होते.तर, परिधान तुलनेने लहान आणि मंद आहे.जेव्हा परिधान एका विशिष्ट स्तरावर पोहोचते, तेव्हा साधन कुचकामी होते आणि जलद पोशाखांच्या कालावधीत प्रवेश करते.
कटिंग टूल्स का आणि कसे चालवायचे आहेत?
आम्ही वर नमूद केले आहे की प्रारंभिक परिधान अवस्थेत, साधन तुटण्याची शक्यता असते.तुटण्याची घटना टाळण्यासाठी, आपण टूलमध्ये धावले पाहिजे.उपकरणाचे कटिंग तापमान हळूहळू वाजवी तापमानापर्यंत वाढवा.प्रायोगिक पडताळणीनंतर, समान प्रक्रिया पॅरामीटर्स वापरून तुलना केली गेली.हे पाहिले जाऊ शकते की धावल्यानंतर, साधनाचे आयुष्य दुप्पट पेक्षा जास्त वाढले आहे.
वाजवी स्पिंडल गती राखून फीडची गती अर्ध्याने कमी करणे ही रन-इनची पद्धत आहे आणि प्रक्रियेची वेळ अंदाजे 5-10 मिनिटे आहे.मऊ पदार्थांवर प्रक्रिया करताना लहान मूल्य घ्या आणि कठोर धातूंवर प्रक्रिया करताना मोठे मूल्य घ्या.
गंभीर साधन पोशाख कसे ठरवायचे?
गंभीर साधन पोशाख निर्धारित करण्याची पद्धत आहे:
1) प्रोसेसिंग आवाज ऐका आणि कठोर कॉल करा;
2) स्पिंडलचा आवाज ऐकणे, स्पिंडल मागे धरण्याची एक लक्षणीय घटना आहे;
3) प्रक्रिया करताना कंपन वाढते आणि मशीन टूल स्पिंडलवर स्पष्ट कंपन असल्याचे जाणवणे;
4) प्रोसेसिंग इफेक्टवर आधारित, प्रक्रिया केलेला तळाचा ब्लेड नमुना चांगला किंवा वाईट असू शकतो (जर सुरुवातीला असे असेल तर, हे सूचित करते की कटिंगची खोली खूप खोल आहे).
मी चाकू कधी बदलू?
आपण टूल आयुर्मान मर्यादेच्या सुमारे 2/3 वर टूल बदलले पाहिजे.उदाहरणार्थ, जर टूलला 60 मिनिटांच्या आत तीव्र झीज होत असेल, तर पुढील प्रक्रियेत 40 मिनिटांच्या आत टूल बदलणे सुरू केले पाहिजे आणि नियमितपणे टूल बदलण्याची सवय लावावी.
कठोरपणे थकलेली साधने मशीन करणे सुरू ठेवू शकतात?
गंभीर साधन परिधान केल्यानंतर, कटिंग फोर्स सामान्यपेक्षा तीन पट वाढू शकते.कटिंग फोर्सचा स्पिंडल इलेक्ट्रोडच्या सर्व्हिस लाइफवर महत्त्वपूर्ण प्रभाव पडतो आणि स्पिंडल मोटर आणि फोर्सच्या सर्व्हिस लाइफमधील संबंध तिसऱ्या पॉवरच्या व्यस्त प्रमाणात आहे.उदाहरणार्थ, जेव्हा कटिंग फोर्स तीन पटीने वाढतो, तेव्हा 10 मिनिटांसाठी प्रक्रिया करणे सामान्य परिस्थितीत 10 * 33 = 270 मिनिटे स्पिंडल वापरण्यासारखे असते.
खडबडीत मशीनिंग दरम्यान टूलची विस्तारित लांबी कशी ठरवायची?
टूलची विस्ताराची लांबी जितकी लहान असेल तितके चांगले.तथापि, वास्तविक मशीनिंगमध्ये, जर ते खूप लहान असेल तर, टूलची लांबी वारंवार समायोजित करणे आवश्यक आहे, ज्यामुळे मशीनिंग कार्यक्षमतेवर मोठ्या प्रमाणात परिणाम होऊ शकतो.तर वास्तविक मशीनिंगमध्ये कटिंग टूलची विस्तारित लांबी कशी नियंत्रित करावी?तत्त्व खालीलप्रमाणे आहे: φ 3 व्यासासह टूलबार 5 मिमी वाढवून सामान्यपणे प्रक्रिया केली जाऊ शकते.φ 4-व्यास कटर बार 7 मिमी वाढवून सामान्यपणे प्रक्रिया केली जाऊ शकते.φ 6-व्यास कटर बार 10 मिमी वाढवून सामान्यपणे प्रक्रिया केली जाऊ शकते.कापताना या मूल्यांच्या खाली पोहोचण्याचा प्रयत्न करा.वरच्या टूलची लांबी वरील मूल्यापेक्षा मोठी असल्यास, टूल परिधान करताना प्रक्रियेच्या खोलीपर्यंत नियंत्रित करण्याचा प्रयत्न करा.हे समजून घेणे थोडे कठीण आहे आणि अधिक प्रशिक्षण आवश्यक आहे.
प्रक्रियेदरम्यान अचानक टूल ब्रेकेज कसे हाताळायचे?
1) मशीनिंग थांबवा आणि मशीनिंगचा वर्तमान अनुक्रमांक पहा.
2) कटिंग पॉईंटवर तुटलेली ब्लेड आहे का ते तपासा आणि असल्यास ते काढून टाका.
3) तुटलेल्या साधनाच्या कारणाचे विश्लेषण करा, जे सर्वात महत्वाचे आहे.साधन का तुटले?वर नमूद केलेल्या प्रक्रियेवर परिणाम करणाऱ्या विविध घटकांचे विश्लेषण करणे आवश्यक आहे.परंतु तुटलेले साधन असे आहे की उपकरणावरील शक्ती अचानक वाढते.एकतर ही पथ समस्या आहे, किंवा जास्त प्रमाणात साधन हलत आहे, किंवा सामग्रीमध्ये कठोर ब्लॉक्स आहेत, किंवा स्पिंडल मोटरचा वेग चुकीचा आहे.
4) विश्लेषणानंतर, प्रक्रियेसाठी साधन पुनर्स्थित करा.जर मार्ग बदलला नसेल तर, मूळ संख्येच्या एक नंबर पुढे मशीनिंग केले पाहिजे.यावेळी, फीड गती कमी करण्यासाठी लक्ष देणे आवश्यक आहे.याचे कारण असे की टूल ब्रेकवर कडक होणे तीव्र असते आणि टूल रनिंग-इन करणे देखील आवश्यक असते.
रफ मशीनिंग चांगले नसताना प्रोसेसिंग पॅरामीटर्स कसे समायोजित करावे?
वाजवी मुख्य अक्षाच्या गतीने टूल लाइफची हमी देता येत नसल्यास, पॅरामीटर्स समायोजित करताना, प्रथम कटिंग डेप्थ समायोजित करा, नंतर फीड गती समायोजित करा आणि नंतर बाजूकडील फीड दर पुन्हा समायोजित करा.(टीप: कटिंग डेप्थ समायोजित करण्यालाही मर्यादा आहेत. जर कटिंगची खोली खूप लहान असेल आणि बरेच स्तर असतील तर, सैद्धांतिक कटिंग कार्यक्षमता जास्त असू शकते. तथापि, वास्तविक प्रक्रियेची कार्यक्षमता इतर घटकांमुळे प्रभावित होते, परिणामी प्रक्रिया खूपच कमी होते. कार्यक्षमता. या टप्प्यावर, प्रक्रियेसाठी कटिंग टूलला लहान साधनाने बदलणे आवश्यक आहे, परंतु प्रक्रियेची कार्यक्षमता जास्त आहे. सर्वसाधारणपणे, किमान कटिंग खोली 0.1 मिमी पेक्षा कमी असू शकत नाही.)
पोस्ट वेळ: एप्रिल-१३-२०२३