CNC-graveringsmaskiner er dyktige i presisjonsbearbeiding med små verktøy og har evnen til å frese, slipe, bore og tappe med høy hastighet.De er mye brukt i forskjellige felt som 3C-industrien, formindustrien og medisinsk industri.Denne artikkelen samler vanlige spørsmål om CNC-graveringsbehandling.
Hva er hovedforskjellene mellom CNC-gravering og CNC-fresing?
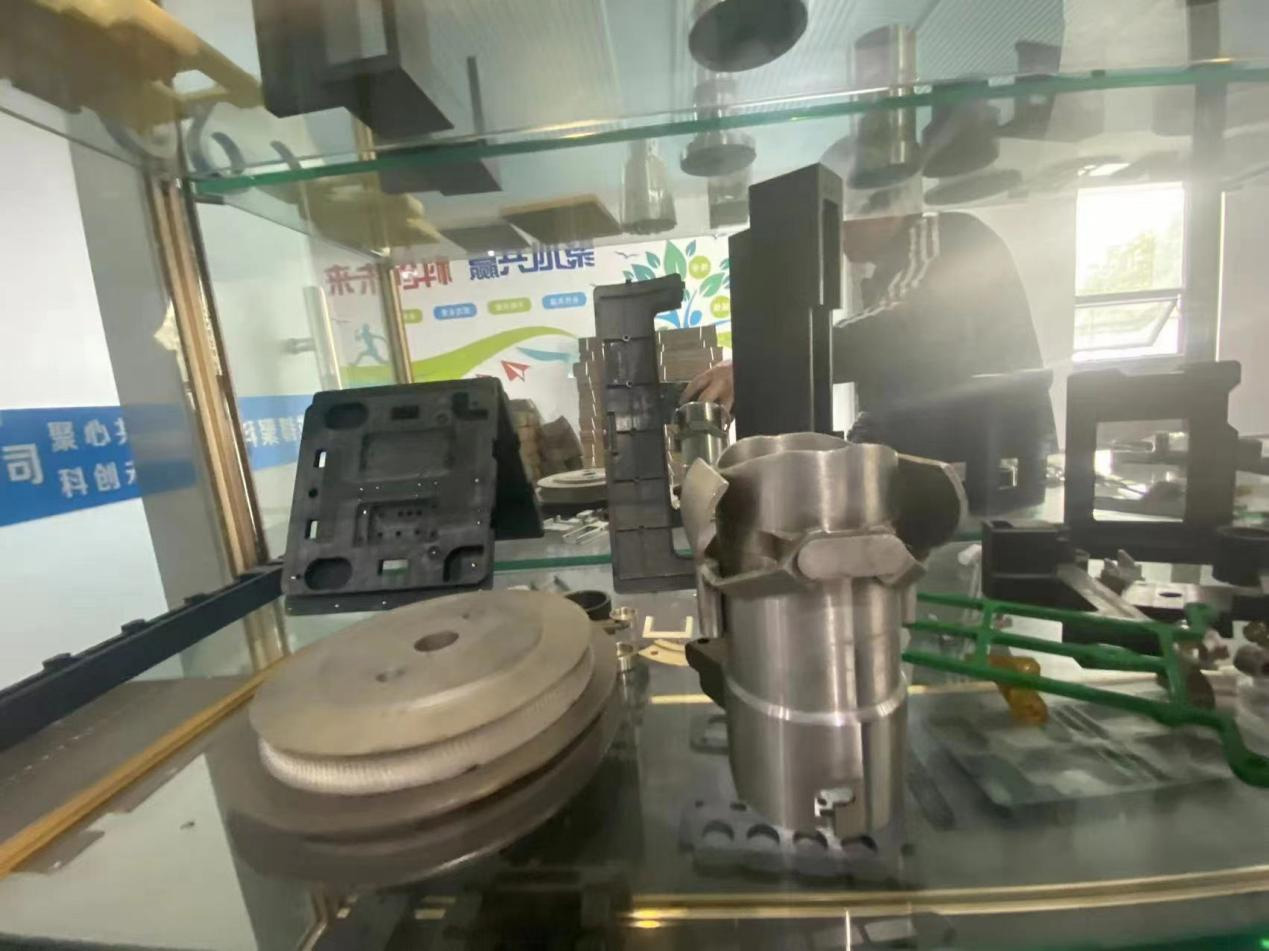
Både CNC-gravering og CNC-freseprosesser bruker freseprinsipper.Hovedforskjellen ligger i verktøydiameteren som brukes, med det vanlig brukte verktøydiameterområdet for CNC-fresing fra 6 til 40 millimeter, mens verktøydiameteren for CNC-graveringsbehandling varierer fra 0,2 til 3 millimeter.
Kan CNC-fresing kun brukes til grovbearbeiding, mens CNC-gravering kun kan brukes til presisjonsbearbeiding?
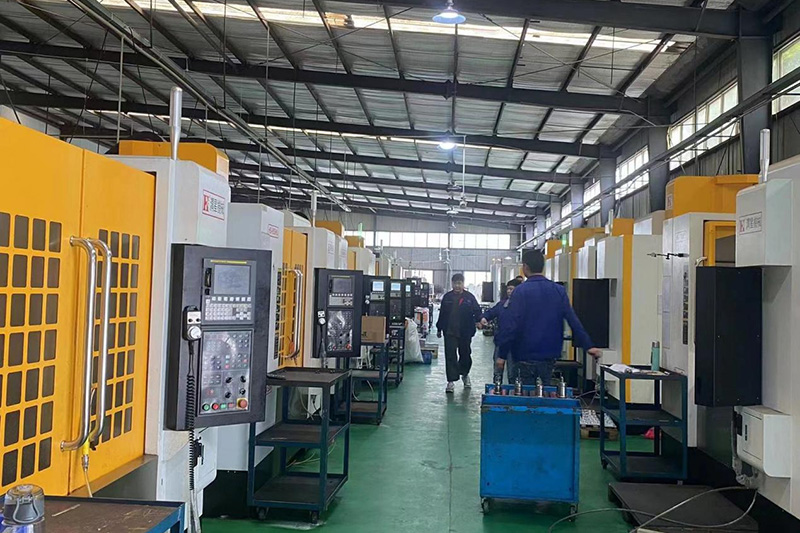
Før vi svarer på dette spørsmålet, la oss først forstå konseptet med prosessen.Behandlingsvolumet for grovbearbeiding er stort, mens prosesseringsvolumet ved presisjonsmaskinering er lite, så noen mennesker betrakter vanligvis grovbearbeiding som "tung skjæring" og presisjonsbearbeiding som "lett skjæring".Faktisk er grov bearbeiding, semi-presisjonsmaskinering og presisjonsmaskinering prosesskonsepter som representerer forskjellige prosessstadier.Så det nøyaktige svaret på dette spørsmålet er at CNC-fresing kan gjøre tung skjæring eller lett skjæring, mens CNC-gravering bare kan gjøre lett skjæring.
Kan CNC-graveringsprosessen brukes til grovbearbeiding av stålmaterialer?
Å bedømme om CNC-gravering kan behandle et bestemt materiale avhenger hovedsakelig av hvor stort verktøy som kan brukes.Skjæreverktøyene som brukes i CNC-graveringsbehandling bestemmer dens maksimale skjærekapasitet.Hvis formen på formen tillater bruk av verktøy med en diameter som overstiger 6 millimeter, anbefales det sterkt å først bruke CNC-fresing og deretter bruke utskjæring for å fjerne gjenværende materiale.
Kan det å legge til et hastighetsøkende hode til spindelen til CNC-maskinsenteret fullføre graveringsprosessen?
Kan ikke fullføre.Dette produktet dukket opp på en utstilling for to år siden, men det var ikke mulig å fullføre utskjæringsprosessen.Hovedårsaken er at utformingen av CNC-bearbeidingssentre vurderer sitt eget verktøyområde, og den generelle strukturen er ikke egnet for graveringsbehandling.Hovedårsaken til denne feilaktige ideen er at de tok feil av den høyhastighets elektriske spindelen som den eneste egenskapen til graveringsmaskinen.
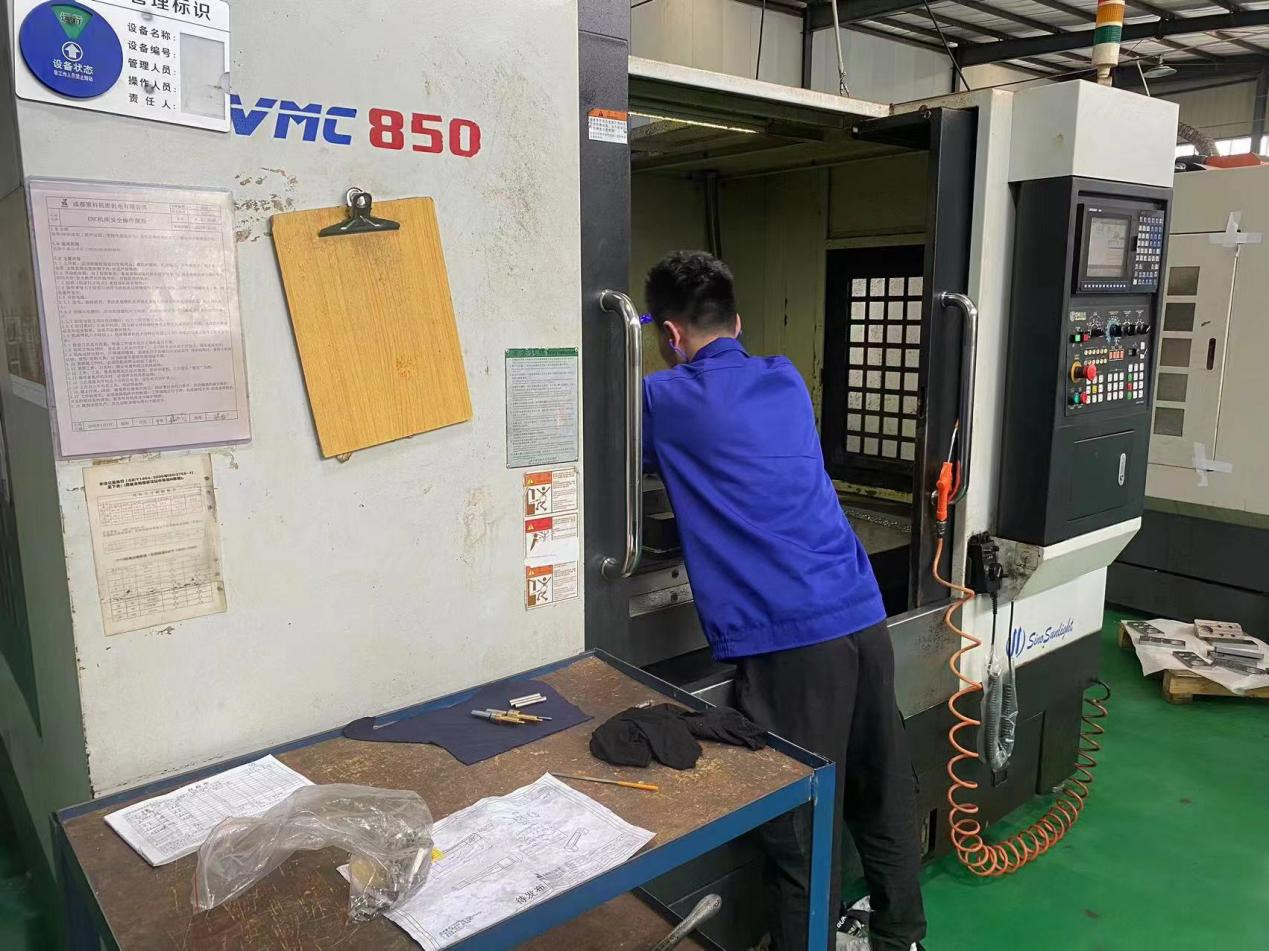
Hva er hovedfaktorene som påvirker utskjæringsbehandlingen?
Mekanisk prosessering er en relativt kompleks prosess, og det er mange faktorer som påvirker den, hovedsakelig inkludert følgende: maskinverktøyegenskaper, skjæreverktøy, kontrollsystemer, materialegenskaper, prosessteknologi, hjelpearmaturer og omgivelsene.
Hva er kravene til kontrollsystemet i CNC-graveringsbehandling?
CNC-graveringsbehandling er først og fremst fresebehandling, så kontrollsystemet må ha evnen til å kontrollere fresebehandlingen.For bearbeiding av små verktøy må fremføringsfunksjonen være tilgjengelig for å bremse banen på forhånd og redusere hyppigheten av verktøybrudd.Samtidig er det nødvendig å øke skjærehastigheten i relativt jevne banesegmenter, for å forbedre effektiviteten av graveringsbehandlingen.
Hvilke egenskaper ved materialer vil påvirke behandlingen?
Hovedfaktorene som påvirker utskjæringsytelsen til materialer er materialtype, hardhet og seighet.Materialkategoriene inkluderer metalliske materialer og ikke-metalliske materialer.Totalt sett, jo høyere hardhet, jo dårligere bearbeidbarhet, mens jo høyere viskositet, jo dårligere bearbeidbarhet.Jo flere urenheter, jo dårligere bearbeidbarhet, og jo større hardhet har partikler inne i materialet, noe som resulterer i dårligere bearbeidbarhet.En generell standard er: jo høyere karboninnhold, jo dårligere bearbeidbarhet, jo høyere legeringsinnhold, jo dårligere bearbeidbarhet, og jo høyere ikke-metallisk elementinnhold, jo bedre bearbeidbarhet (men ikke-metallisk innhold generelt materialer er strengt kontrollert).
Hvilke materialer er egnet for utskjæringsbehandling?
Ikke-metalliske materialer som er egnet for utskjæring inkluderer organisk glass, harpiks, tre osv. Ikke-metalliske materialer som ikke er egnet for utskjæring inkluderer naturlig marmor, glass osv. Egnede metallmaterialer for utskjæring inkluderer kobber, aluminium og mykt stål med en hardhet mindre enn HRC40 , mens uegnede metallmaterialer for utskjæring inkluderer bråkjølt stål, etc.
Hva er virkningen av selve skjæreverktøyet på maskineringsprosessen og hvordan påvirker det det?
Skjæreverktøyfaktorene som påvirker graveringsprosessen inkluderer verktøymateriale, geometriske parametere og slipeteknologi.Skjæreverktøymaterialet som brukes i utskjæringsprosessen er hardt legeringsmateriale, som er en pulverlegering.Hovedytelsesindikatoren som bestemmer materialets ytelse er pulverets gjennomsnittlige diameter.Jo mindre diameteren er, desto mer slitesterkt er verktøyet, og jo høyere vil verktøyets holdbarhet være.Mer NC-programmeringskunnskap fokuserer på WeChat offisielle konto (NC-programmeringsundervisning) for å få veiledningen.Skarpheten til verktøyet påvirker hovedsakelig skjærekraften.Jo skarpere verktøyet er, desto lavere skjærekraft, desto jevnere er bearbeidingen, og jo høyere overflatekvalitet, men jo lavere holdbarhet har verktøyet.Derfor bør forskjellig skarphet velges ved bearbeiding av forskjellige materialer.Når du behandler myke og klebrige materialer, er det nødvendig å skjerpe skjæreverktøyet.Når hardheten til det behandlede materialet er høy, bør skarpheten reduseres for å forbedre holdbarheten til skjæreverktøyet.Men den kan ikke være for sløv, ellers vil skjærekraften bli for stor og påvirke bearbeidingen.Nøkkelfaktoren i verktøysliping er maskestørrelsen til presisjonsslipeskiven.En høymasket slipeskive kan produsere finere skjærekanter, og effektivt forbedre holdbarheten til skjæreverktøyet.Slipeskiver med høy maskevidde kan gi jevnere flankeoverflater, noe som kan forbedre overflatekvaliteten på skjæringen.
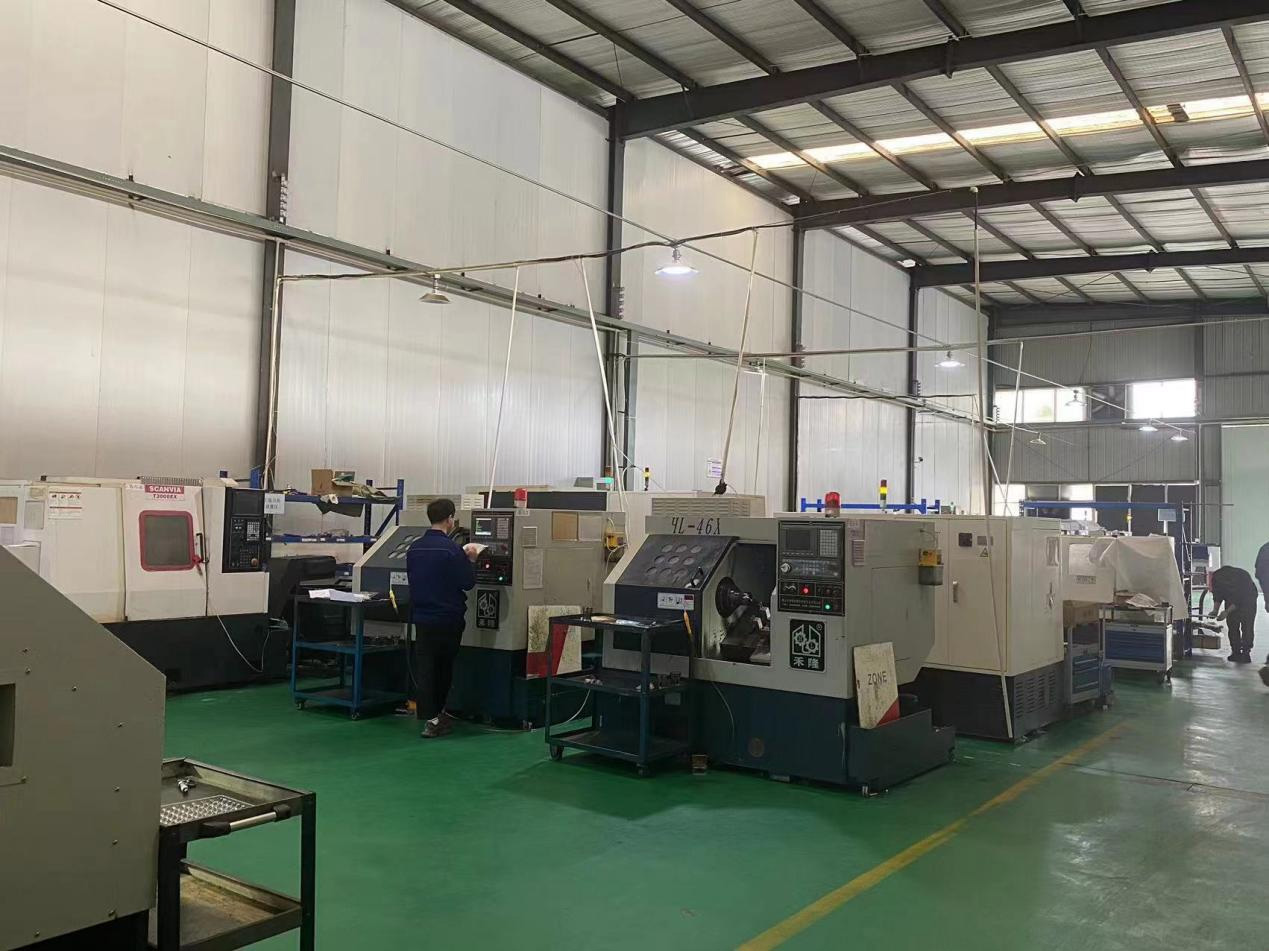
Hva er formelen for verktøylevetid?
Verktøylevetiden refererer hovedsakelig til verktøylevetiden under bearbeiding av stålmaterialer.Den empiriske formelen er: (T er verktøyets levetid, CT er levetidsparameteren, VC er skjærelinjehastigheten, f er skjæredybden per omdreining, og P er skjæredybden).Skjærelinjehastigheten har størst innvirkning på verktøyets levetid.I tillegg kan verktøyets radiale utløp, verktøyslipekvalitet, verktøymateriale og belegg og kjølevæske også påvirke verktøyets holdbarhet.
Hvordan beskytte utskjæringsmaskinutstyr under behandlingen?
1) Beskytt verktøyinnstillingsenheten mot overdreven oljeerosjon.
2) Vær oppmerksom på kontrollen av flygende rusk.Flyvende rusk utgjør en stor trussel mot maskinverktøyet.Å fly inn i det elektriske styreskapet kan forårsake kortslutning, og å fly inn i styreskinnen kan redusere levetiden til skruen og styreskinnen.Derfor, under behandlingen, bør hoveddelene av maskinverktøyet forsegles ordentlig.
3) Når du flytter belysningen, må du ikke trekke i lampelokket, da det lett kan skade lampedekselet.
4) Under maskineringsprosessen må du ikke nærme deg skjæreområdet for observasjon for å unngå flyvende rusk som kan skade øynene.Når spindelmotoren roterer, er det forbudt å utføre noen operasjon på arbeidsbenken.
5) Når du åpner og lukker maskinens dør, må du ikke åpne eller lukke den med makt.Under presisjonsmaskinering kan støt og vibrasjoner under døråpningsprosessen forårsake knivmerker på den behandlede overflaten.
6) For å gi spindelhastigheten og deretter starte behandlingen, ellers på grunn av den trege starten av spindelen, kan det hende at ønsket hastighet ikke nås før behandlingen starter, noe som kan føre til at motoren kveles.
7) Det er forbudt å plassere verktøy eller arbeidsstykker på verktøymaskinens tverrbjelke.
8) Det er strengt forbudt å plassere magnetiske verktøy som magnetiske sugekopper og måleklokkeholdere på det elektriske kontrollskapet, da dette kan skade skjermen.

Hva er funksjonen til kuttevæske?
Vær oppmerksom på å tilsette kjøleolje under metallbearbeiding.Funksjonen til kjølesystemet er å fjerne skjærevarme og flyvende rusk, og gir smøring for maskinering.Kjølevæsken vil flytte skjærebåndet, redusere varmen som overføres til skjæreverktøyet og motoren, og forbedre levetiden.Ta bort flyvende rusk for å unngå sekundær kutt.Smøring kan redusere skjærekraften og gjøre maskineringen mer stabil.Ved bearbeiding av kobber kan bruk av oljeholdig skjærevæske forbedre overflatekvaliteten.
Hva er stadiene av verktøyslitasje?
Slitasjen til skjæreverktøy kan deles inn i tre stadier: innledende slitasje, normal slitasje og skarp slitasje.I det innledende slitasjestadiet er hovedårsaken til verktøyslitasje at verktøytemperaturen er lav og ikke når den optimale skjæretemperaturen.På dette tidspunktet er verktøyslitasjen hovedsakelig abrasiv slitasje, som har større innvirkning på verktøyet.Mer NC-programmeringskunnskap fokuserer på WeChat offisielle konto (digital kontroll programmering undervisning) for å motta opplæringen, som er lett å forårsake verktøybrudd.Dette stadiet er svært farlig, og hvis det ikke håndteres riktig, kan det direkte føre til brudd på verktøyet og feil.Når verktøyet passerer den innledende slitasjeperioden og skjæretemperaturen når en viss verdi, er hovedslitasjen diffusjonsslitasje, som hovedsakelig forårsaker lokal avskalling.Så slitasjen er relativt liten og sakte.Når slitasjen når et visst nivå, blir verktøyet ineffektivt og går inn i en periode med rask slitasje.
Hvorfor og hvordan må skjæreverktøy kjøres inn?
Vi nevnte ovenfor at under det første slitasjestadiet er verktøyet utsatt for brudd.For å unngå fenomenet brudd må vi kjøre inn verktøyet.Øk skjæretemperaturen til verktøyet gradvis til en rimelig temperatur.Etter eksperimentell verifisering ble sammenligninger gjort ved bruk av de samme prosesseringsparametrene.Man ser at etter innkjøring har verktøyets levetid økt med mer enn det dobbelte.
Innkjøringsmetoden er å halvere matehastigheten samtidig som man opprettholder en rimelig spindelhastighet, og behandlingstiden er ca. 5-10 minutter.Når du behandler myke materialer, ta den lille verdien, og når du behandler harde metaller, ta den store verdien.
Hvordan bestemme alvorlig verktøyslitasje?
Metoden for å bestemme alvorlig verktøyslitasje er:
1) Lytt til prosesseringslyden og foreta en hard samtale;
2) Når du lytter til lyden av spindelen, er det et merkbart fenomen med spindelen som holder tilbake;
3) Følelse av at vibrasjonen øker under bearbeiding, og det er tydelig vibrasjon på maskinverktøyspindelen;
4) Basert på prosesseringseffekten kan det behandlede bunnbladmønsteret være bra eller dårlig (hvis dette er tilfellet i begynnelsen, indikerer det at skjæredybden er for dyp).
Når bør jeg bytte kniv?
Vi bør erstatte verktøyet ved rundt 2/3 av verktøyets levetid.For eksempel, hvis verktøyet opplever alvorlig slitasje innen 60 minutter, bør neste behandling begynne å skifte verktøyet innen 40 minutter og utvikle en vane med å skifte verktøyet regelmessig.
Kan sterkt slitte verktøy fortsatt bearbeides?
Etter sterk verktøyslitasje kan skjærekraften øke til tre ganger det normale.Kuttekraften har en betydelig innvirkning på levetiden til spindelelektroden, og forholdet mellom levetiden til spindelmotoren og kraften er omvendt proporsjonal med tredje potens.For eksempel, når skjærekraften øker med tre ganger, tilsvarer bearbeiding i 10 minutter å bruke spindelen i 10 * 33=270 minutter under normale forhold.
Hvordan bestemme forlengelseslengden på verktøyet under grovbearbeiding?
Jo kortere forlengelseslengden på verktøyet er, jo bedre.Men ved faktisk maskinering, hvis den er for kort, må lengden på verktøyet justeres ofte, noe som kan påvirke maskineringseffektiviteten i stor grad.Så hvordan skal forlengelseslengden på skjæreverktøyet kontrolleres i faktisk maskinering?Prinsippet er som følger: φ En verktøystang med en diameter på 3 kan behandles normalt ved å forlenge 5 mm.φ Knivbjelken med 4 diameter kan behandles normalt ved å forlenge 7 mm.φ Skjærebjelken med 6 diameter kan behandles normalt ved å forlenge 10 mm.Prøv å nå under disse verdiene når du skjærer.Hvis lengden på det øvre verktøyet er større enn verdien ovenfor, prøv å kontrollere det til behandlingsdybden når verktøyet slites.Dette er litt vanskelig å få med seg og trenger mer trening.
Hvordan håndtere plutselig brudd på verktøyet under bearbeiding?
1) Stopp bearbeidingen og se det gjeldende serienummeret til bearbeidingen.
2) Sjekk om det er et ødelagt blad ved skjærepunktet, og fjern det i så fall.
3) Analyser årsaken til det ødelagte verktøyet, som er det viktigste.Hvorfor gikk verktøyet i stykker?Vi må analysere fra de ulike faktorene som påvirker behandlingen nevnt ovenfor.Men årsaken til det ødelagte verktøyet er at kraften på verktøyet plutselig øker.Enten er det et baneproblem, eller det er overdreven verktøyristing, eller det er harde blokker i materialet, eller spindelmotorhastigheten er feil.
4) Etter analysen, bytt ut verktøyet for behandling.Hvis banen ikke er endret, bør bearbeidingen utføres ett nummer foran det opprinnelige nummeret.På dette tidspunktet er det nødvendig å være oppmerksom på å redusere matehastigheten.Dette er fordi herdingen ved verktøybruddet er kraftig, og det er også nødvendig å utføre verktøyinnkjøring.
Hvordan justere prosessparametere når grovbearbeiding ikke er bra?
Hvis verktøyets levetid ikke kan garanteres ved en rimelig hovedaksehastighet, må du justere skjæredybden først ved justering av parametere, deretter justere matehastigheten og deretter justere sidematingshastigheten igjen.(Merk: Justering av skjæredybden har også begrensninger. Hvis skjæredybden er for liten og det er for mange lag, kan den teoretiske skjæreeffektiviteten være høy. Den faktiske bearbeidingseffektiviteten påvirkes imidlertid av andre faktorer, noe som resulterer i for lav bearbeiding effektivitet. På dette tidspunktet er det nødvendig å erstatte skjæreverktøyet med et mindre for bearbeiding, men bearbeidingseffektiviteten er høyere. Generelt sett kan minimum skjæredybde ikke være mindre enn 0,1 mm.).
Innleggstid: 13-apr-2023